The Accessible Farm Shop: Usable and Efficient
Ned Stoller, B.S., ATP
Shawn Ehlers Ph.D., ATP
Richard Brzozowski Ph.D.
This publication was made possible by USDA/NIFA Special Project 2021-41590-34813.
Introduction
The farm shop is often the headquarters of the farming operation. Repairs, maintenance, fabrication, inventory storage, business decisions, and even hobbies are often conducted in this location. As workers grow older and eventually develop medical conditions, or if younger workers sustain injuries or illnesses that impair their ability to do necessary tasks, having an accessible farm shop that is usable and efficient improves the likelihood of success for the farm business. Because the farm shop is so critical to the success of many farms and ranches, designs for accessibility should be implemented when remodeling or building new facilities.
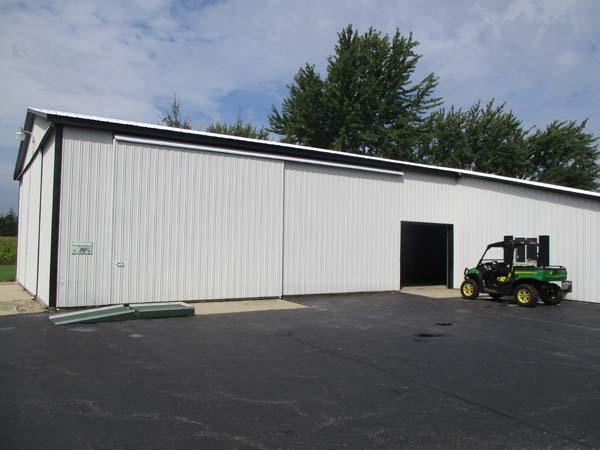
Figure 1. Careful planning of the farm shop can make it accessible and usable for all individuals with and without medical impairments.
Creating a space that accommodates the demands of the worker(s) is essential to farm shop accessibility, safety, and efficiency. The term “farm shop” is used to refer to any facility on a farm, ranch, or other agricultural workplace where maintenance or service work is done. Begin planning for enhanced farm shop accessibility by considering the necessary tasks undertaken throughout the year. Determine the location, size, and features of the shop based on that task list. After the building structure is designed, plan the layout of the workspaces and storage areas in the shop, including office, living spaces, and toilet facilities as needed. Furnish the farm shop with adapted tools and equipment that enable farmers and ranchers with disabilities to complete their work. Modern “smart” home technologies, such as smart fire alarms, remote cameras, carbon monoxide detectors, thermostats, door controllers, and virtual AI assistants will likely play a role. These accessibility principles and a little ingenuity can make farm shops useable and efficient for most workers, regardless of age or disability.
Location
Begin by choosing the best farm shop location and structure based on its expected uses and workers’ abilities. A farmer or rancher is apt to go in and out of the shop more times than any other building on the farmstead except the house. Therefore, the shop should be located for convenient
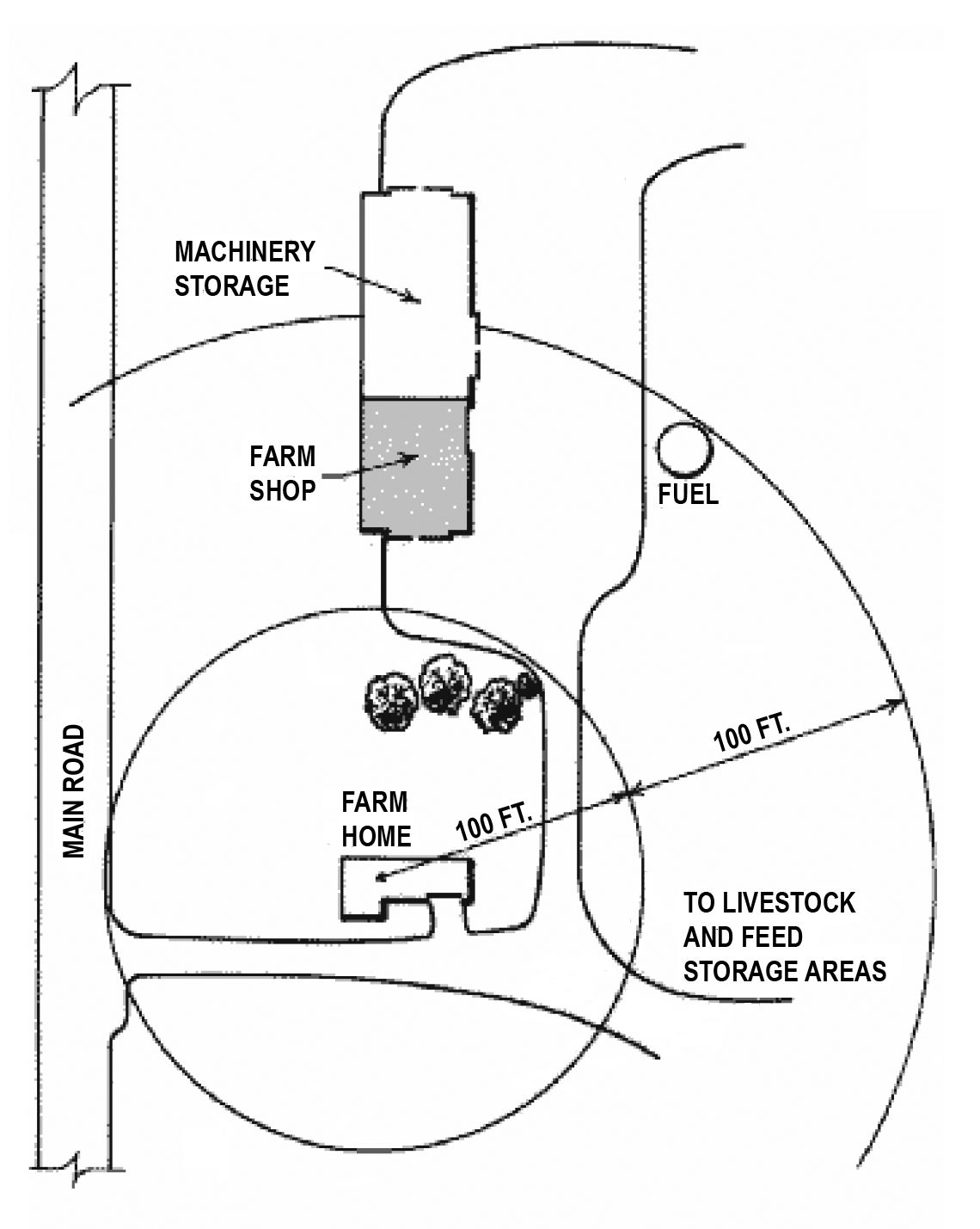
Figure 2. The shop should be convenient to the farm home and to vehicle traffic. The circular zones, 100 feet apart, show how the shop fits into the rest of the farmstead.
access from the home, machinery storage, and the primary farm traffic routes. Because of the high value of shop tools, security should be a major consideration in site selection. (Friday, et.al, 1980). Position the shop as close as possible to the home without decreasing the quality of life in the home or preventing movement of larger equipment. Make clear smooth pathways directly from the house to the shop that are easy to access (and will accommodate snow removal equipment in northern climates). The shop should be at least 50 feet away from other buildings to keep a possible fire from spreading. (Lechner, et.al., 1981). Some farmers or ranchers with mobility impairments have created living spaces connected directly to the farm shop for maximum accessibility, including a kitchen, shower, and toilet facilities. This is especially important when the farm shop is located at a site away from home.
Expected uses
To better determine its location on the farm, the size of the building, and how it is organized, make a list of both short- and long-term expected uses for the farm shop. If building a new shop or expanding an existing one, the farm shop should be positioned so that regular tasks do not cause a negative impact on the home. Examples include pressure-washing smelly manure spreaders, cutting and grinding metal while others are sleeping, or welding and creating noxious fumes. The shop and its doors will need to be large enough to fit machinery inside for repairs with walkways around it so workers can safely move about and reach the required tools and supplies. Consider a detailed shop task list over the course of a year. For example:
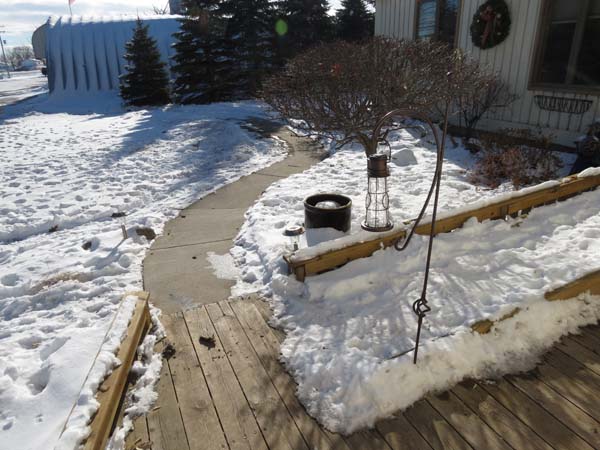
Figure 3. Make clear smooth pathways directly from the house to the shop that are easy to access with snow removal equipment.
- Will the shop be primarily used for doing repairs? Fabrication? Painting? Equipment storage? Office? etc., …
- Do workers have physical conditions that make it difficult to do jobs in the current farm shop?
- Are alternative farm enterprises or diversification opportunities considered that will need shop space?
- Is insulation needed for year-round use, or will it be used only in mild weather?
- Will heat and/or air conditioning be an asset?
- Is the shop accessible to the largest equipment currently owned and to equipment that is planned to be purchased?
- Is a second level needed for overflow storage?
- Will floor drains be needed for equipment to be washed inside and to trap pollutants?
- How much workbench space and stationary equipment is needed (welder, drill press, etc.)?
- Will ventilation fans be needed to expel fumes?
- Is a crane needed for heavy lifting?
Figure 4. What tasks need done in the shop? Can tools be easily reached? Will equipment fit in the space for repairs or will it end up outside?
Renovate or build new?
The choice between renovating an existing facility or building a new farm shop is a significant business decision. A new shop allows for progressive planning and more accessibility features such as widened doors, improved heating and cooling, and more natural light from windows. For some operations, an existing shop can be upgraded and/or expanded to adequately meet the changing needs of the operation. Regardless, a careful inventory is needed that addresses both the current and anticipated needs. For example, a 4-inch reinforced concrete floor worked well for smaller equipment, but 6- to 8-ton tractors in common use today will soon damage these thinner floors. Many older shops were wired with 30-amp, 120-volt service, which no longer accommodates some new stationary power tools, including welders or electric vehicle charging stations.
The list of expected uses and the budget will prioritize improvements to existing farm shops. Renovating an existing building will generally cost less and take less time than building new. Extending the length of a building is the most cost-efficient way to increase space because sidewalls can be lengthened, and additional trusses added without significant
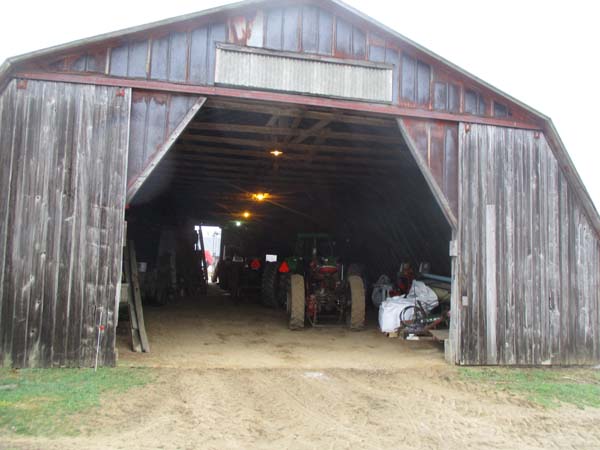
Figure 5. Renovating an existing building may be the only good option from a financial perspective, but upgrades can be very expensive.
redesigning of the structure. If an existing shop building needs an increase in width or height or a repaired foundation,, then it is more appropriate to build new. Framing and insulating one area of an existing machinery storage building for year-round shop work can be a practical renovation. However, while a shop located at one end of an existing machinery storage building may give convenient access to stored equipment, a separate shop building makes future expansion easier for both the shop and the storage buildings. (Friday, et.al, 1980).
The many benefits of building a new farm shop include adequate space for work and storage, accommodation for personal needs, creating an efficient workflow, incorporating the latest electronic/computer technologies, energy efficiency, and providing multipurpose space. A new building can be a great step forward toward accessibility, work efficiency, and safety in the farm shop if it is within the budget. Progressive or chronic medical conditions such as multiple sclerosis and rheumatoid arthritis (and also the natural aging process) will decrease a worker’s physical abilities and should be considered during the farm shop planning process. Caution is advised against being too conservative in planning that could result in not accounting for future accessibility needs that seem, at the moment, like current wants.
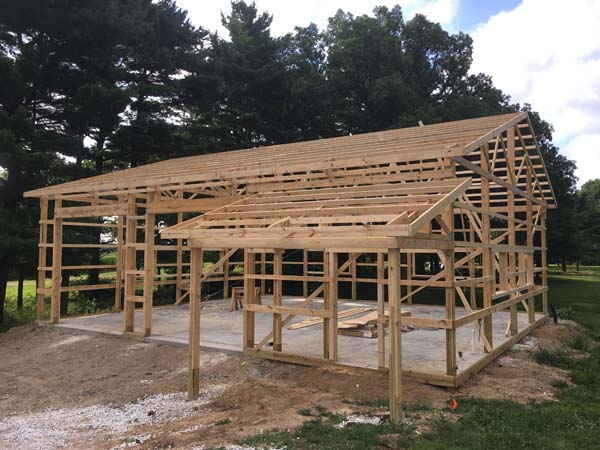
Figure 6. Building a new farm shop is a good choice if the existing shop building will not accommodate equipment or is structurally unsound.
The budget for the farm shop will determine if optional features can be included after current needs and anticipated expansions are addressed. To design a shop with features that “would be really nice to have” – but would not improve future accessibility – might not be the best business decision. Having a smaller, more accessible building that is better equipped with appropriate tools could be a better choice for usability. In this sense, do not confuse needs and wants. However, remember that the goal of planning is to have a farm shop where workers can safely and efficiently complete the necessary tasks.
Structure
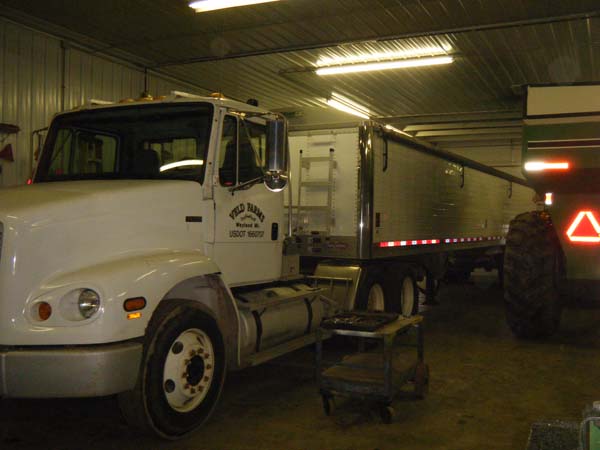
Figure 7. Size the shop to fit the largest equipment that is planned to be repaired plus 5-feet space for working. Plan for future growth as your equipment will likely be larger within 10 years.
A crowded, disorganized farm shop will be difficult for workers, especially those with mobility impairments, to work in. Physically measure the length, width, and height of equipment to plan the best building size. Most row-crop machinery shops are constructed with 18-foot-tall entry doors to accommodate combines. Building “up” provides a low-cost upper level for inventory storage. However, upper floors might not be accessible by workers with impaired mobility or balance without an elevator. Make the workspace for repairs large enough to allow the longest equipment to drive all the way in, allowing the door to be closed. Adequate space for tool and supply storage near the work area is needed to reduce walking.
When remodeling an existing building, it is usually most cost-effective to add length; therefore, getting the height and width right the first time is a must. In southern climates work is often done under a roof for shade without sidewalls. This provides extra space around equipment and a cooling breeze but is difficult to secure.
Floors
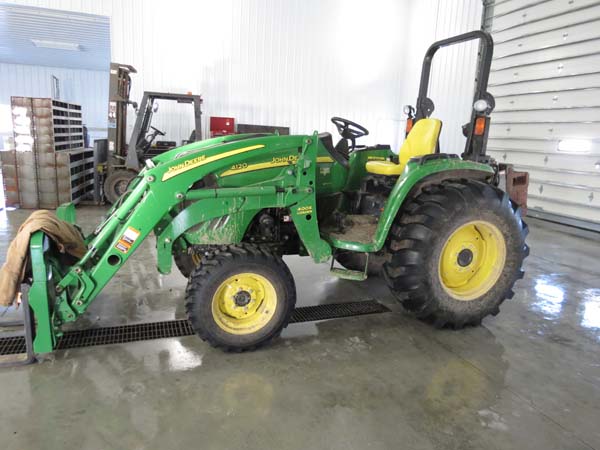
Figure 9. Properly sloped floors and adequate floor drains play a crucial role in reducing slip hazards. Use metal floor drain grates rated to support heavy machinery.
Uncluttered concrete floors provide flat, firm surfaces to walk on without tripping or limiting mobility aids. Smooth finishes on new concrete are easier to clean, while textured floors are slip-resistant. Surface treatments for concrete make it less permeable to oil/gas spills, but they can create very slippery surfaces when wet. A vapor barrier installed below the floor before installing concrete and proper building ventilation will reduce slippery moisture problems on the shop floor, especially in cold weather. Surface expansion joints should be added at a minimum of every 10 feet to direct cracks should settling occur over time. Uneven floors caused by cracking and settling are trip hazards, so proper thickness and reinforced concrete installation that meet local building code specifications are important. (Bundy & Harmon, 2009).
A concrete outdoor approach apron 4 feet wider than the door and extending 16 feet out from the building provides a smooth surface to park machinery for emergency repairs and washing. The apron should slope away from the building a minimum of 1/8 inch per foot to provide drainage. (Friday, et.al, 1980). In some areas of the country these outside work areas are shaded to provide additional protected workspace.
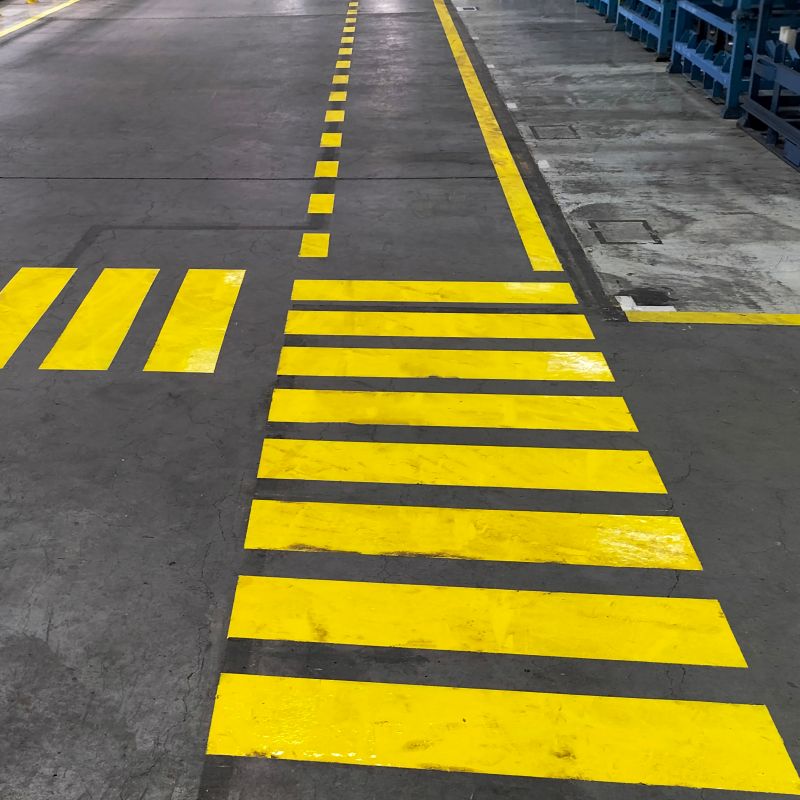
Figure 10. Floor markings keep travel areas clear and can assist workers with low vision when backing equipment into storage or service areas.
Markings on the floor in the service areas help those with low vision or memory loss to correctly position equipment in the shop for repairs. Clearly marked pathways on the floor between workspaces and tool storage areas prevent trip hazards and obstructions for workers with mobility impairments. Electric cords and air hoses are common trip hazards on workspace floors, and workers with hand and arm impairments can have difficulty rolling them up. Some re-wind reels are spring-loaded to quickly roll up electric cords or hoses and keep floors clear.
Water supply and drains
A water supply and drains are necessary for machine maintenance and personal health. Having clean water for drinking and washing are important for hygiene. Unheated shops can use frost-free hydrants to supply water to utility sinks and for washing machinery. Local building codes specify frost-free burial depth of water lines. While it is common to place water lines under the concrete floor, it is very difficult for future maintenance should they corrode or freeze.
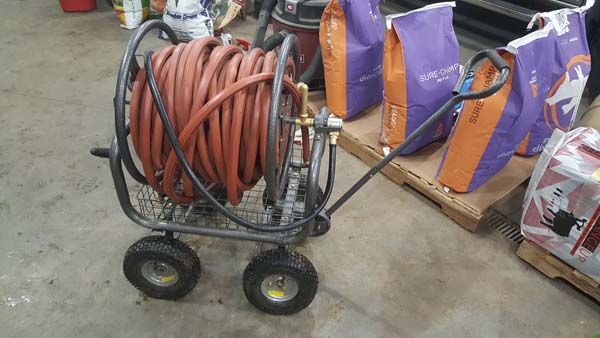
Figure 11. Use a hose reel on wheels to easily store the hose
and move it to a warm storage location.
Floors in wash areas should be textured and be sloped to drains approximately ⅛ to ¼ inch per foot. (Friday, et.al, 1980). It is critical to have cleanable grates positioned over adequately sized drains to remove water when pressure-washing equipment indoors. Engine-driven pressure washers should never be used inside the shop due to the risk of carbon monoxide exposure. Electric-powered washers should be considered. A catch basket in the drains for accidentally dropped items, such as fasteners, small parts, or jewelry, is also recommended.
Wall and ceiling material
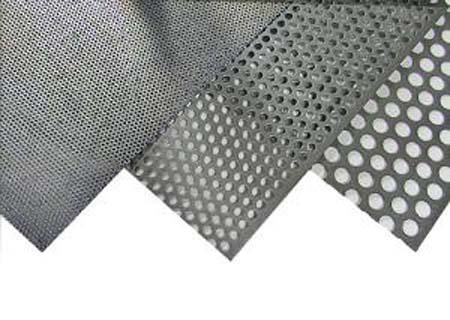
Figure 12. Wood or perforated steel panels help
deaden sound in the farm shop.
Wall and ceiling materials can impact workers with low vision and hearing loss. Metal walls and ceilings are often used in farm shops for fire safety and durability. White metal is a good choice for workers with low vision because the light reflectance of metal walls makes the farm shop brighter. However, metal walls will make the shop much louder and more difficult to hear in for those with hearing impairments. Sound-deadening, perforated, acoustical steel panels can be installed on the ceiling and areas of the shop where water and fire hazards do not exist. Choose appropriate wall and ceiling material for the shop based on the attributes in the following chart. If there are plans to eventually heat the shop, both wall and ceiling insulation should be installed. Vapor barriers and insulated walls and ceilings of the farm shop provide user comfort, lowers costs of heating/cooling, and reduces condensation.
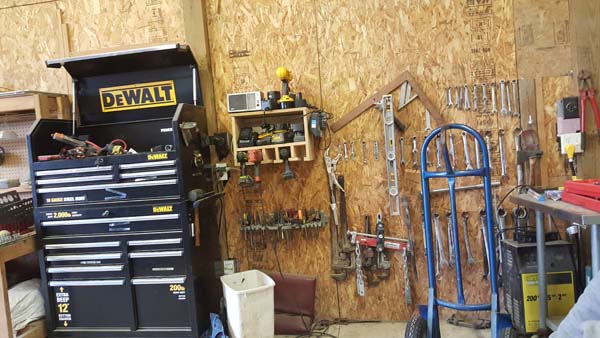
Figure 13. Wood walls make organizing tools easy! Obvious visible tool placement
enhances access and reduces clutter.
TABLE 1. WALL MATERIAL TYPES
Material type | Pros | Cons |
Wood | Inexpensive; durable; paintable; sound-deadening; convenient for hanging tools | Low light reflectance, ease of cleaning, and fire retardancy; possible pest infestation; water permeable |
Metal | Pre-colored (bright white has high light reflectance); easy to install; pest resistant; durable; fire retardant; water resistant; easy to clean | Costly; noisy – may need sound-deadening panels |
Drywall | Inexpensive; paintable; sound deadening; fire retardant; pest resistant | Labor intensive; water permeable; low ease of cleaning; prone to damage |
Vinyl | Inexpensive; pre-colored; pest resistant; water resistant; ease of installation; ease of cleaning | Low heat resistance; difficult to repair; brittle when cold |
Heating and cooling
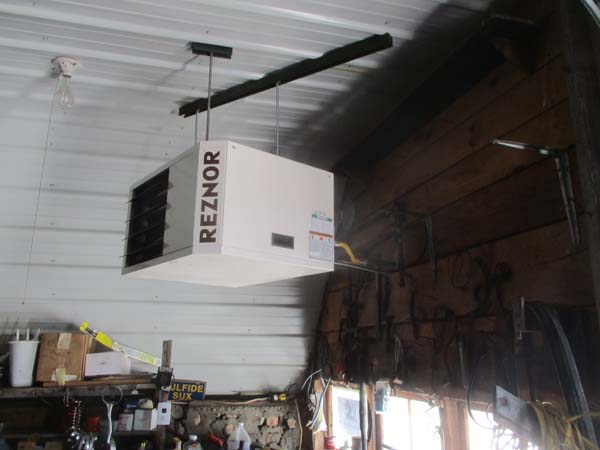
Figure 14. This well-insulated farm shop has gas heat. Fire resistant metal wall material should be installed around heat sources.
Extreme temperature exposure can drain energy from workers with arthritis and limited endurance. A heated and/or cooled area of the farm shop can alleviate this limitation. Workers can spend winter days in a heated shop doing maintenance and repairs on equipment to prepare it for the next growing season. Wood is a low-cost fuel but may be difficult for some workers to lift and carry. Unit heaters can be the most economical and accessible workshop heat source. They are permanently suspended from the shop ceiling or wall and typically fueled by propane or natural gas. In-floor heat is an efficient option for new construction but is expensive. Electric heat pumps work well in moderate mid-south and southern climates. They cost more to install but are energy efficient for heating and cooling and they are relatively quiet.
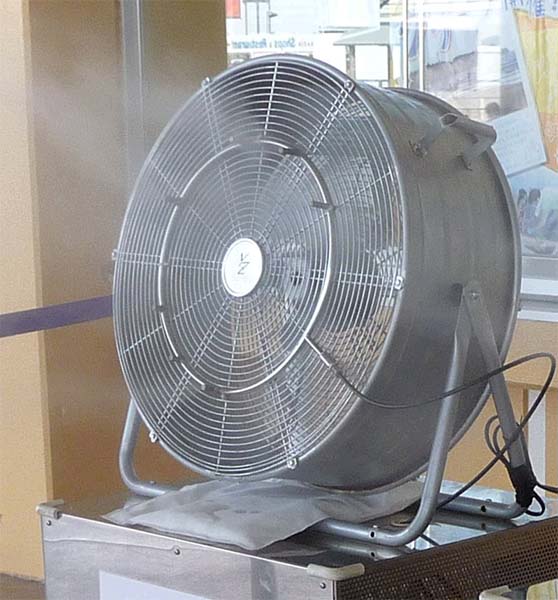
Figure 15. Portable cooling/misting fans work by both creating wind movement and dispensing water vapor, giving the feeling of up to a 30-degree temperature drop.
Cooling can be accomplished by fans, window air conditioners, central air units for the whole building, or by portable misting fans. Misting fans are especially helpful for people with difficulty regulating body temperature who need to continue working in hot weather. Evaporative cooling systems, or “swamp coolers” can be
effective but work best in dry climates. Evaporative cooling vests can be worn while working in a hot place and provide personal cooling. In hot climates, take advantage of prevailing breezes through window and door placement.
Ventilation
Ventilation provides air exchange, bringing fresh air into the building (OSHA, 1999). Whether the source of pollution is from a welder, blowing off equipment, painting, or a large tractor engine running in the shop, there needs to be adequate ventilation to prevent exposure to fumes and carbon monoxide poisoning. In some instances, the contaminant source may be the outside air, (OSHA, 1999), for example a tractor idling outside an open shop window. Relying on outside air for ventilation from improperly placed inlet fans may bring contaminants into the workplace.
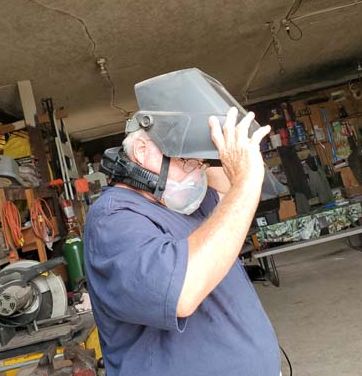
Figure 17. When adequate ventilation cannot be achieved for the workspace, powered air purifier
respirators like the Cleanspace respirator will filter fumes and dust from the air for an individual worker. CAUTION: PAPR systems will not protect from oxygen deficient environments or prevent
carbon monoxide poisoning!
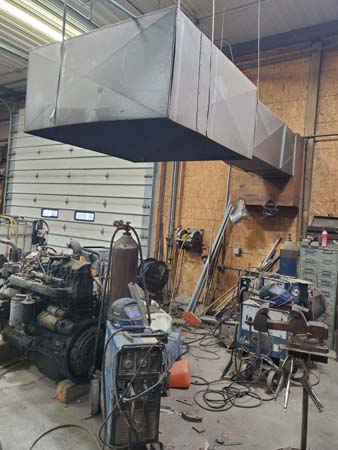
Figure 16. Ventilation hoods can be mounted over the metalworking workbench, or flexible ventilation tubes moved to those sites where welding is going to be done.
Exhaust hoods in welding areas are necessary to remove smoke and fumes. Most important is a wall-mounted exhaust fan with about 1,000 cfm capacity for each welding worktable. (Friday, et.al, 1980). Vehicle exhaust systems draw smoke directly from engine exhausts or mufflers and blow it outside. Painting areas also need to be well ventilated, warm, dry, and positioned away from heat/ignition sources. A separate ventilated room or area of the shop is needed for frequent painting.
Powered air-purifying respirators (PAPR) are wearable personal systems that use a battery-powered fan to draw ambient air through a HEPA filter and blow it into the mask for the worker to breathe. However, personal protective equipment such as this should be last resort, and structural ventilation should be relied on to remove dust and fumes from the shop, especially for workers with respiratory impairments.
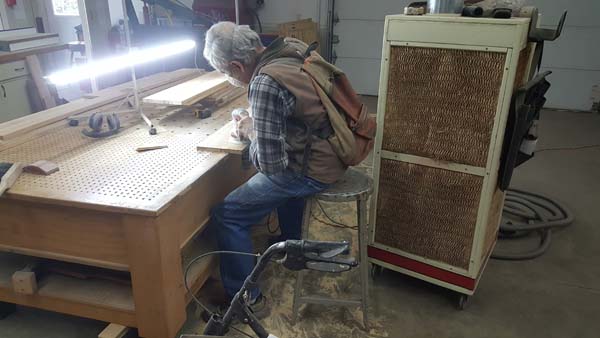
Figure 18. Air cleaner systems draw dusty air through filters and blow the clean air back into the room but require regular maintenance. This table has a vacuum that draws dust down through the holes and into a filter.
Windows and doors
Large doors are required on farm shops to allow large equipment access to the building. Powered door openers allow workers with limited upper limb use, back injuries, or reduced strength to open and close doors. Sliding doors are the most common and low-cost doors found in use on shops because they are sturdy and cover large openings. They are, however, difficult to push due to their heavy weight and wind pressure. Powered sliding door systems now come with options to make them remote-control operated. Overhead doors are very convenient to open with a remote power opener.
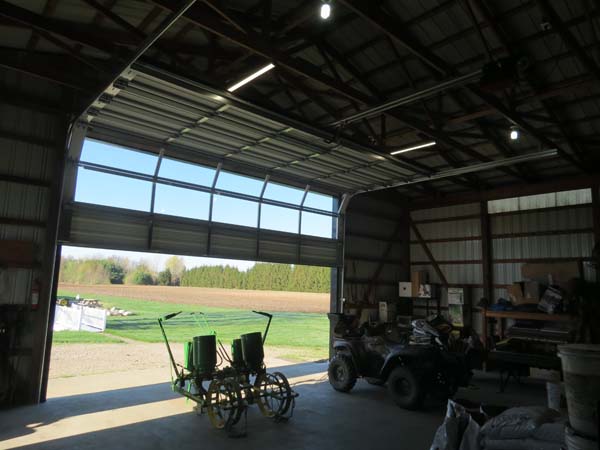
Figure 20. A segmented overhead door with windows and power opener provides natural light and remote control.
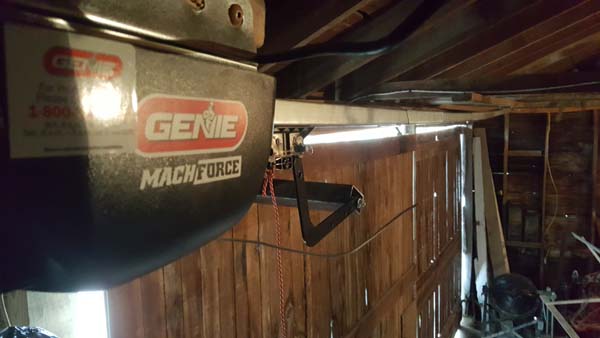
Figure 19. Standard garage door openers can be adapted with custom brackets to open sliding doors.
TABLE 2. FARM SHOP DOOR TYPES
Machinery Door Style | Pros | Cons |
Sliding Track Door | Least expensive; custom fit to opening; can be equipped with electric opener; no loss in headroom | Heavy/difficult to manually move; limited insulation capability; may block other entrances; can be blocked by snow; usually no windows |
Side-Hinged Door | Custom fit; can be equipped with electric opener; no loss in headroom | Limited width; large opening swing; hinge strain increases with width; can be blocked by snow |
Overhead Door (segmented) | Can be insulated; can be equipped with electric opener; optional windows; available widths up to 40’ | Decreases ceiling clearance; may obstruct ceiling-mounted lights; can be expensive |
Hydraulic & Bifold Lift Doors | Large; heavy duty; can be insulated; swings outward; creates covered space outside when open; extremely wide widths; no loss in headroom; optional windows | Most expensive; single-panel hydraulic doors can be blocked by snow |
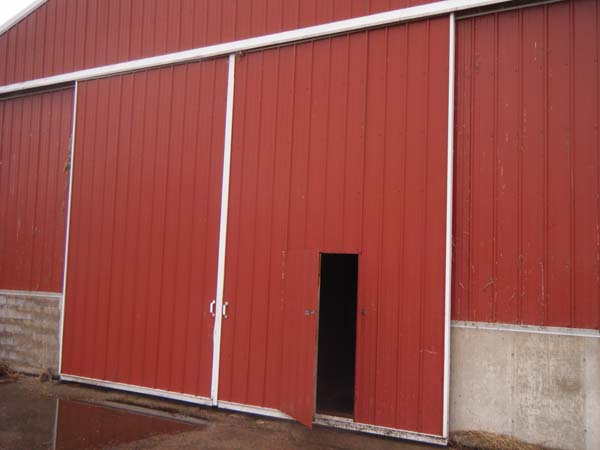
Figure 21. Sliding doors are low cost but may be hard to open and block other parts of the building. A walk-through door designed in the sliding door can allow personal access without opening the
heavier large door.
Walk-through service doors are generally the most frequently used doors in the farm shop. New farm shops should be built with doors at ground level, so ramps are not needed for wheelchair entry. A door window provides natural light and clear view of approaching visitors. Service doors 36-inches wide with lever handles are most easy to open for all workers. Multiple access doors on large shops can save a lot of walking to access the different areas of the shop and provide additional emergency exits. All doors designated as emergency exits should be clearly identified with signage and not locked from the inside. Ramps should meet ADA standards with 12:1 slope and 1/2″ maximum thresholds.
Numerous windows in the shop provide much appreciated natural light into the work area. Place them low enough that workers can see out from a seated position. Select windows and doors for energy efficiency and the ability to be easily opened for ventilation.
Lighting
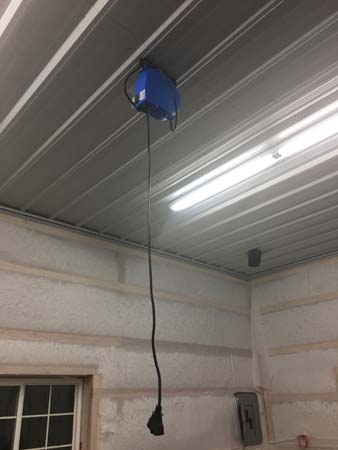
Figure 24. LED is most efficient light source currently available, does not have a “strobe effect”, and has a wide operating temperature range.
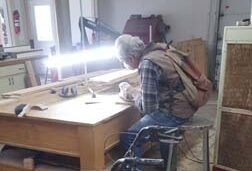
Figure 23. This farmer created an adjustable-height LED light stand to improve visibility in his farm shop.
Adequate lighting is perhaps one of the most important factors to consider in the farm shop regarding work performance and safety, especially for workers with low vision. Proper placement of light sources is key to reducing shadowing effects caused by large machinery. Portable lights are useful when working in awkward places. Please refer to the AgrAbility technical report titled “Lighting for Farmsteads and Self-propelled Agricultural Machinery” (www.agrability.org/resources/technical-reports-plowshares) for greater detail on the subject. The use of LED lighting has been shown to be the most energy efficient, though initially more expensive.
Electrical
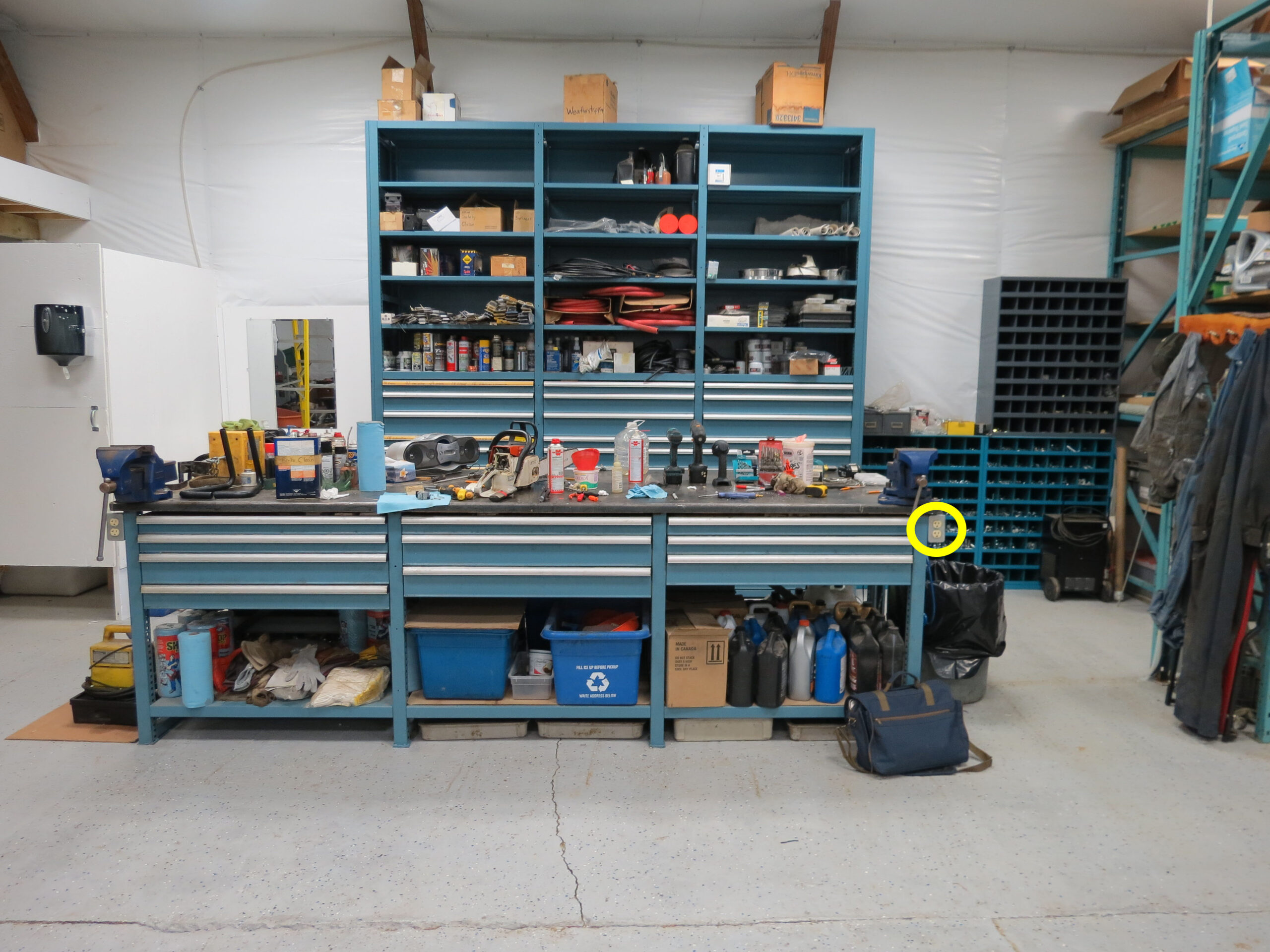
Figure 25. An electrical outlet on the front side of this work bench gives convenient access to power without using extension cords.
Modern farm shops rely heavily on electrical power, so having a general idea of present and future electrical needs is important. Consult a licensed electrician to plan service. A 200-amp, 220V electrical service is typical for modern farm shops. Dedicated circuit components, such as air conditioning and heat, large air compressors, cranes, metalworking tools, and water heaters are wired directly to the breaker box. The 220V receptacles should be strategically placed for such items as a welder or air compressor and should be near a window for a potential air-conditioner.
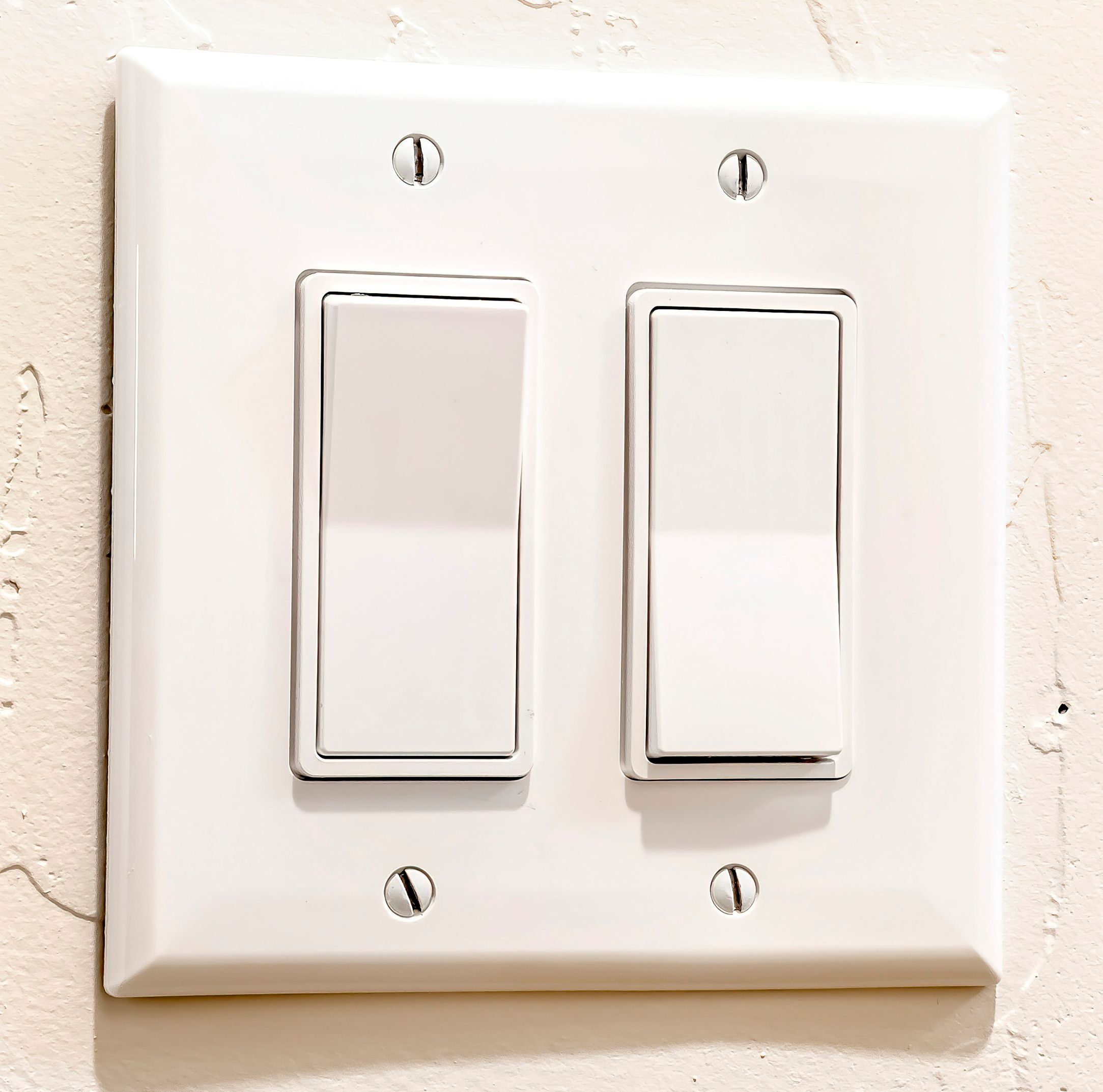
Figure 26. Flat rocker panel light switches provide greater access for workers with hand impairments.
Place 110V receptacles 6-feet apart at workbench height near workspaces for convenience and safety. With better access to outlets, workers will need fewer extension cords, decreasing the likelihood of trips and fire hazards. Safety is further increased with auto-retracting power cords from the ceiling. Wiring outlets on several different circuits from the main panel will prevent overloading and tripping breakers. Always use GFCI outlets near wet work areas and outdoor work areas.
Compressed air
Compressed air is a necessity for inflating tires, cleaning parts, and powering pneumatic tools. Many shops are converting to battery-operated tools to reduce the clutter of air hoses. Because air hoses are a trip hazard on shop floors, plumb permanent air lines around the shop walls with quick-connects in multiple locations to limit the amount of
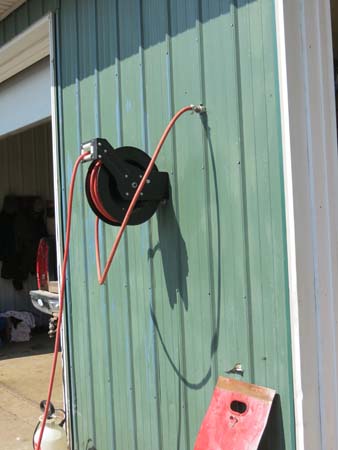
Figure 27. Auto rewind air-line storage reels make it easier for workers with arm impairments to store hoses. They are often mounted on the ceiling or side walls to reduce tripping hazards.
hose needed to reach service areas. Most farm shops use ½-inch iron, copper, or aluminum alloy pipes. Do not use PVC or plumb airlines in interior wall cavities. Ensure that air compressor controls and tank drains are easily accessible for proper maintenance. Auto rewind air-line storage reels make it easier for workers with upper limb impairments to store hoses. They are often mounted on the ceiling to reduce tripping hazards. Air hose quick connects may also be useful on exterior walls for outdoor projects.
Overhead cranes and service pits
Overhead cranes greatly reduce the potential for back strain in a farm shop and are invaluable for farmers and ranchers with disabilities. They are, however, a significant investment and need to be planned for during construction. They are used to remove heavy loads out of trucks, pull engines from machinery, and lift heavy parts into place. These cranes need to be secured solidly to the farm shop structure including reinforced concrete for bolting the base to the floor and reinforced vertical pillars. Consultation from an engineer may be needed for supporting cranes. It should be noted that the trusses found in typical farm pole barns are not designed to support vertical loads and should not be used to mount overhead cranes.
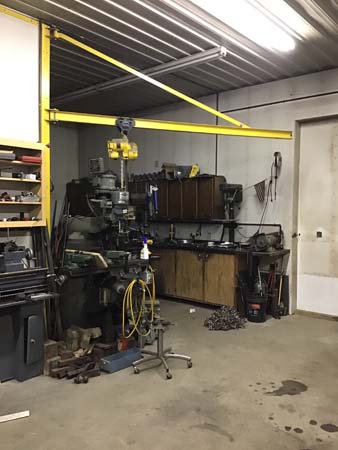
Figure 28. This jib crane is mounted on a corner
so it can swing 270 degrees around the shop.
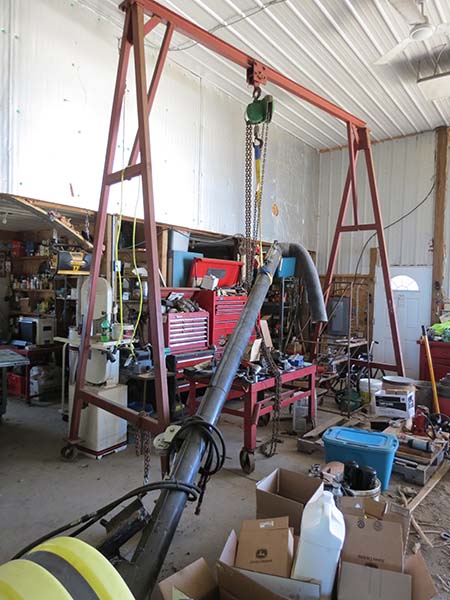
Figure 29. Gantry crane with rolling worktable
underneath it.
Overhead lifts are used to raise vehicles and smaller machinery so a worker can do maintenance without lying down on the floor. A gantry crane is a freestanding A-framed structure on wheels with a trolley and hoist. It can be used to lift heavy loads and can be moved around the shop as needed. A forklift or tractor loader often serves as a hoist in the farm shop. These are convenient because they can be moved while loaded and removed from the shop when not needed. NOTE: Working below a lifting device that does not utilize interlocks to prevent inadvertent lowering of the object can result in injury or death.
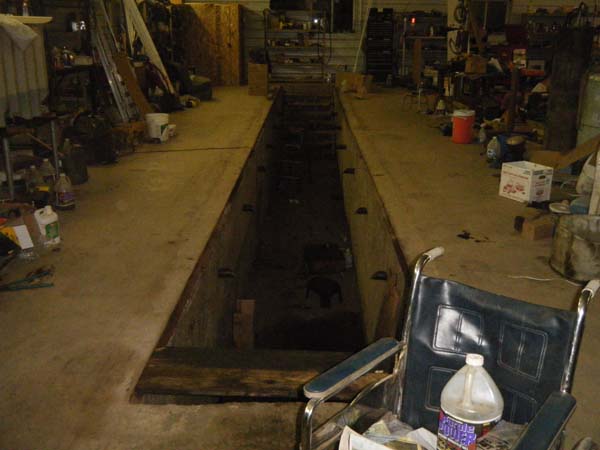
Figure 31. Planning for a service pit, lift or hoist is required during the initial planning and construction of the building to complete excavation and place anchor points.
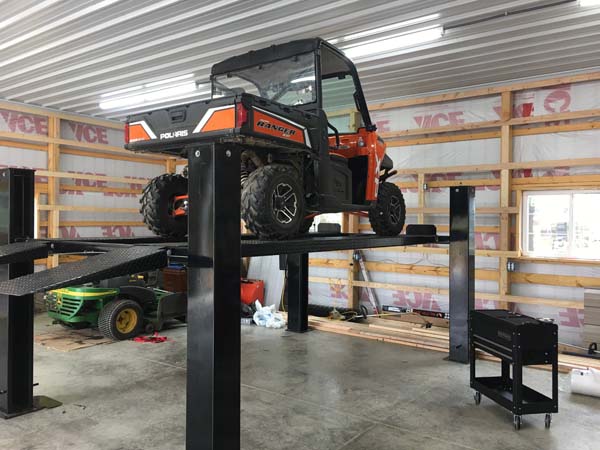
Figure 30. Workers with leg and back impairments can do their own mechanic work when they do not need to crawl under vehicles. Note the rolling tool cart.
Service pits are alternatives for overhead lifts when heavy machinery cannot be raised overhead for service. Machinery is driven over the pit to allow for convenient access to the underside. Auxiliary lighting is needed in the pit along with adaptive technology to enable workers with mobility impairments to access the pit. Safety covers or railings to prevent falls are needed when the pit is not in use.
Organizing the Farm Shop
The farm and ranch shop will be most accessible with well-planned tool selection, workspace layout, and supply storage. Decide how to organize the shop before construction based on the expected task list throughout the year. For example, the floor plan will be significantly different if the focus of the shop is fabricating and painting machines instead of rebuilding engines. Common tools are used frequently for multiple tasks, while specialized tools are only used periodically for very specific, yet important, purposes. Workspaces are areas of the shop planned for a certain type of work to be done such as equipment repairs, metalworking, or office business tasks. Appropriate tools and supplies are grouped in each workspace. Supply storage includes maintenance items like engine oil used on a regular basis, equipment repair parts such as bearings kept in stock for fixing breakdowns, and general supplies kept on hand such as paint and chains. Well organized tools, workspaces, and supplies makes the shop efficient for workers to use.
Using tools
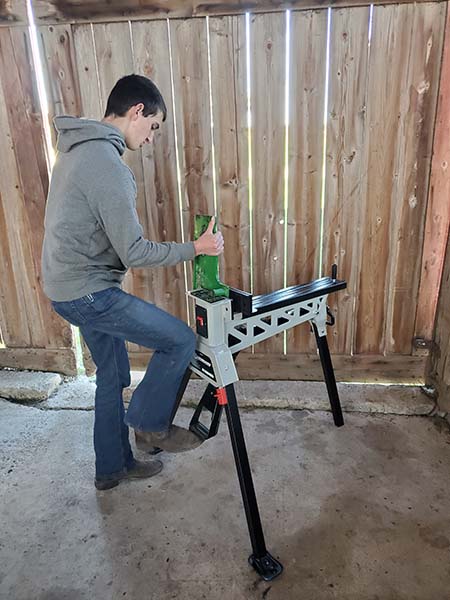
Figure 32. Foot-operated vise clamps are especially helpful.
Tools are used to do all types of work in the shop, but workers with physical limitations, illnesses, or aging conditions will need additional tools in their toolboxes. For workers with hand and arm impairments, clamps are essential. Quick clamps that are easily adjusted to hold work items in place allow an individual to work effectively with his/her good arm. Larger cushioned grips help workers with arthritis hold tools more securely and can be easily provided by wrapping pipe foam insulation or tool handle wrap around a tool handle. Velcro grip gloves secure a weakened hand in a tight fist for lifting with minimal muscle use.
Shop gloves protect workers with sensitive skin from cuts and abrasions. The Toolbox at www.agrability.org/toolbox includes other adaptive tools and aids for working in the shop.
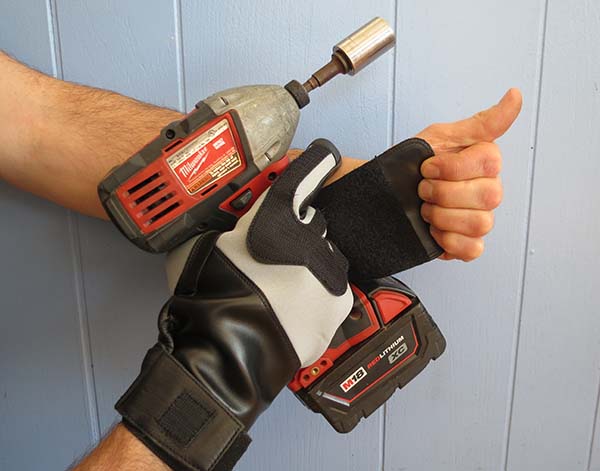
Figure 34. Velcro grip gloves hold the
hand in a tight fist without exerting
muscle strain. This can be helpful when
holding shop tools for long times. This
18V impact driver is a flexible tool for
removing fasteners quickly.
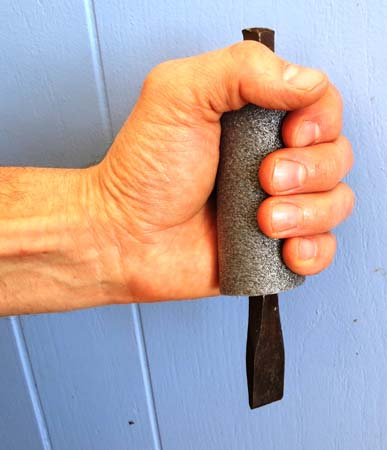
Figure 33. Hand tools with larger cushioned grips and wearing anti-vibration gloves help workers with
carpal tunnel and hand impairments.
Battery-operated tools
Battery-operated tools are rapidly replacing pneumatic and corded power tools. Tools ranging from drills, grinders, and saws to impact nut drivers are lighter, easier to handle, and free from tangled air hoses or electric cords. Such tools can replace ratchet wrenches and brooms and eliminate repetitive motions. Battery operated power tools help workers with reduced strength and endurance. Repetitive motion injuries from twisting wrenches, hammering, or greasing equipment can be avoided and arthritis pain relieved by using these convenient power tools.
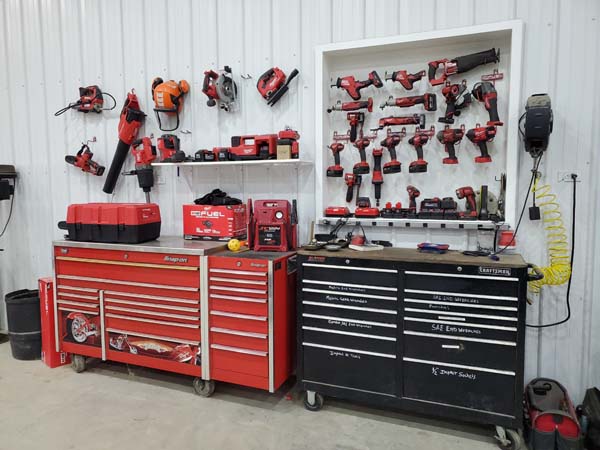
Figure 35. Cordless power tools have been developed for many applications.
Drones are becoming more common on both small and large farm operations saving labor and providing accessibility for security, observing livestock, and scouting fields. They can also be used to inspect tall equipment and structures like grain bins. Drones and many other devices have rechargeable batteries. While battery-powered devices are very helpful, they need to be properly cared for and kept charged. The farm shop should have a clean “low dust” charging place to store rechargeable devices. Also consider a designated parking area for drones. (Bausch, 2023). Batteries should be stored in a clean, temperature-controlled, dry place away from flammable materials. Old and damaged batteries should be recycled as they could be a fire hazard.
Tool storage
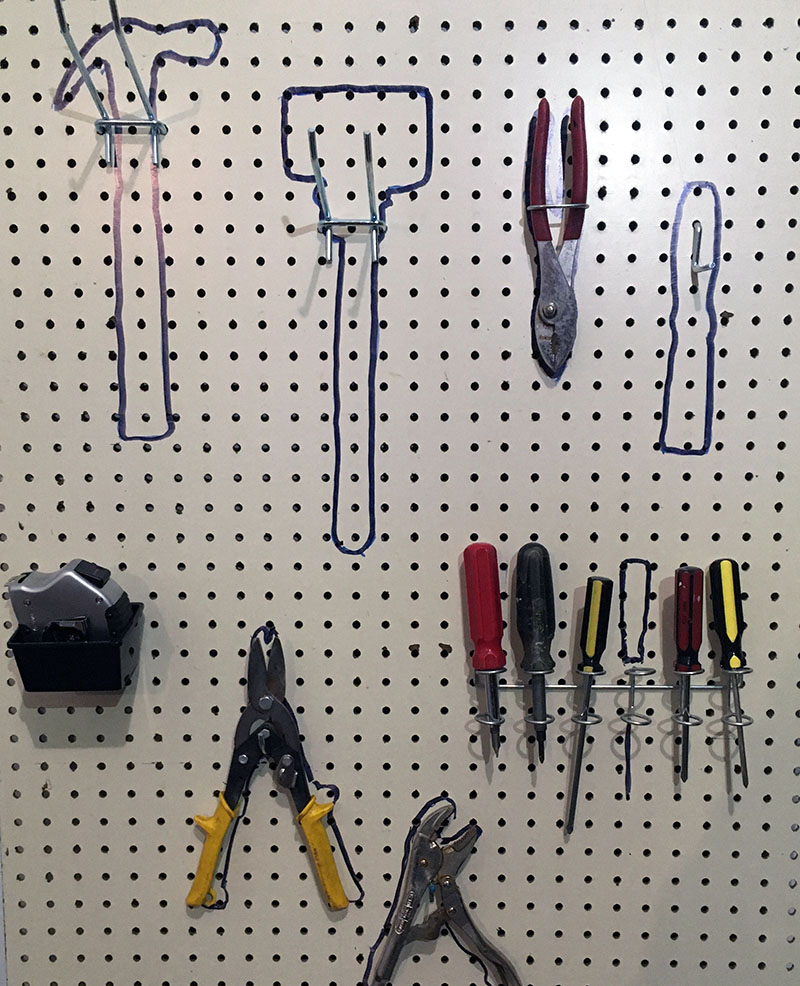
Figure 37. Outlines of tools on a
pegboard help workers know where
to return tools for regular storage.
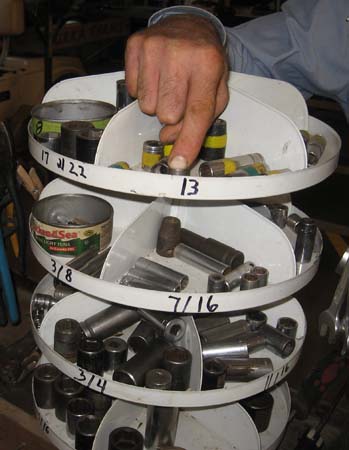
Figure 36. Storing tools in color
coded visible places makes it
easy to put them away.
Tool storage is especially important when multiple workers use the same shop space and one or more of them have a disability. Anyone can waste time searching for tools instead of doing work, but it is a much bigger challenge for someone with mobility impairments or low vision to expend precious energy roaming around the shop in search of the right tool. Clearly mark storage locations, even color-coding tools and racks, to make it easy to return tools to their places. INSERT FIGURE 32 Group specialized tools for specific uses in the appropriate work area on hanging racks to make them easy to find. (Lechner, et.al., 1981). For example, store mechanic tools near the hoist or service pit (marked with yellow tape), and welding clamps and slag hammers on the welding table (marked with green tape).
Common tool carts with hanging tools are highly visible and can be rolled to the appropriate workspace. Freestanding mobile workbenches with additional tools and batteries can be positioned adjacent to the task and eliminate the need to walk to wall-mounted racks. They can be accessed from all sides. If tools from other areas of the shop are accumulated while working on a project, they can be loaded on a cart and easily returned to their proper storage location with minimal lifting and carrying. Everyone benefits when every tool is returned to its designated place, clean and unbroken, after use.
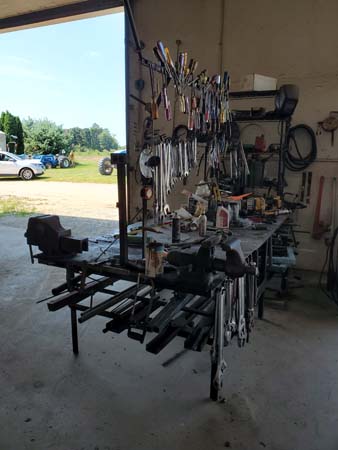
Figure 40.
Freestanding
mobile workbenches
with
hanging tools
are positioned
adjacent to the
task and reduce
the need for
multiple trips
to toolbox. They
can be accessed
from all sides.
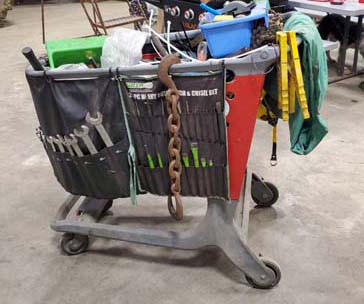
Figure 39. Rolling tool carts with hanging
tools can be clearly seen and eliminate
the need to make repeated trips to wall-mounted racks.
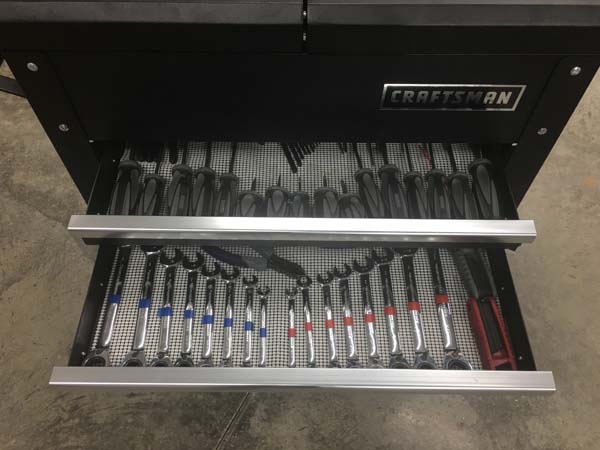
Figure 38. Colored coded SAE and Metric wrenches is especially helpful, but closed drawers hide contents from people with memory loss.
Workspaces
Workspaces are dedicated areas of the shop planned for a certain type of work to be done with a large, unobstructed floor space for free movement around the task. Most farm and ranch shops have workspaces for equipment repairs, metalworking, and office business tasks. Other workspaces might be set aside for rebuilding engines, woodworking, or painting. Specialized tools and supplies are grouped in each workspace and organized on easily reached shelves and racks. (Lechner, et.al., 1981). Appropriate equipment, workbenches, pneumatic and electrical power supplies, high-quality lighting, and proper ventilation must be present in each workspace.
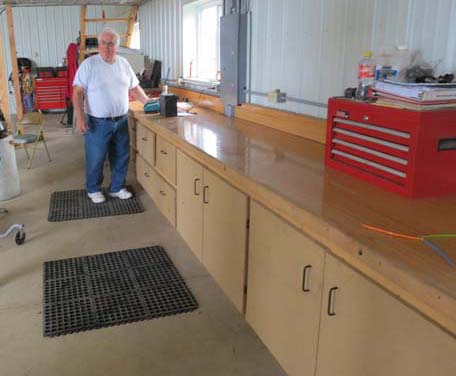
Figure 41. Floor cushions in the workspace relieve
hip and back pain. Note electrical outlets above
the work bench.
The maintenance/repair workspace for machinery and implements is the primary use for most farm and ranch shops and often includes the overhead crane or service pit. An open area around the repaired equipment allows rolling tool carts and mobility aids to access the best location. If space allows, create an open area in the shop for quicker service projects and another workspace for longer-term, major repairs. Portable lighting, electrical outlets, air hose connections, and vehicle exhaust ventilation systems will be important in this workspace. Workers with mobility impairments or memory loss will benefit by having a list of tools and supplies used for each regular maintenance task. An example would be, “changing the oil on the Chevy pickup requires a 15mm wrench for the drain plug, an FIL7060 oil filter, oil drain pan, filter wrench, shop rags, and 5 quarts of 5W30 engine oil”. This prevents all the effort of rolling under the truck only to find out the 5/8” wrench is the wrong size tool. Such records can be stored on smartphone apps, computer spreadsheets, or paper notebooks in a filing cabinet.
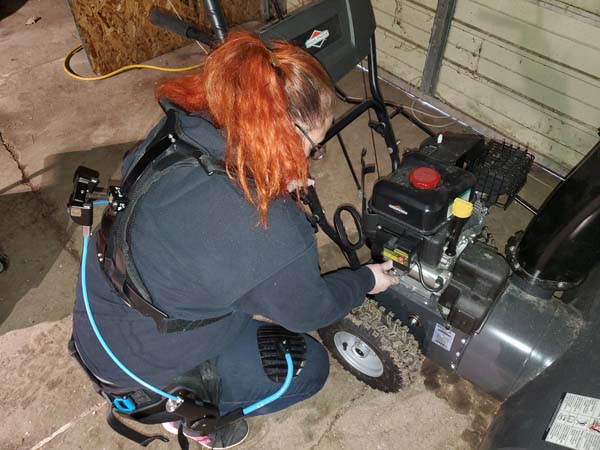
Figure 42. Wearable exoskeletons can support a
person’s back or shoulders while doing shop work.
Ergonomic work positioning in the workspace with an adjustable height stool and table is important for people with musculoskeletal disorders. Wearable exoskeletons are spring-loaded devices that support weakened muscle groups in the back and arms and help with bending, lifting, and reaching. Many tasks in the farm shop cannot be done at a workbench. Mechanic creepers help roll under equipment for service. (National AgrAbility Project, 2011). Workers with hip and knee impairments might not be able to kneel down to get on a creeper, so power-lift creeper seats may be needed. Top-side creepers provide comfortable positioning when leaning over the top of an engine compartment. Rolling shop ladders have handrails and steps with better footing than stepladders for workers with leg impairments (see figure 4). (National AgrAbility Project, 2011). Workers using wheelchairs need to roll under and/or around workbenches to reach the surfaces without bumping their legs or feet.
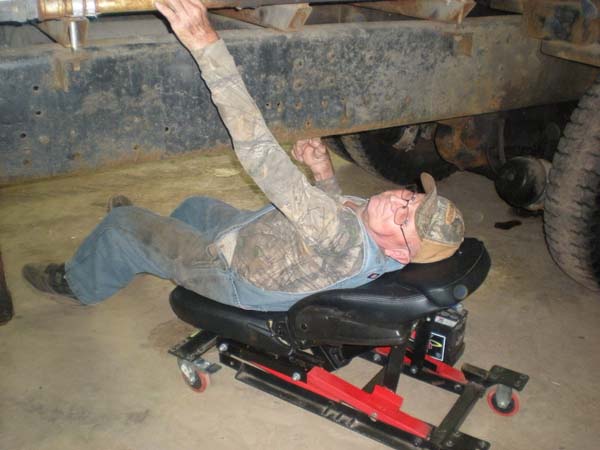
Figure 43. This 12V powered work positioning seat reclines and powers up and down.
Workers with medical conditions may struggle to lift and move heavy parts around the shop. Hydraulic lift table carts raise and lower heavy loads for ergonomic positioning and roll from place to place easily. A basic “cherry picker” engine hoist is a small, flexible crane on wheels with many uses for lifting smaller loads.
The metalworking workspace is where broken parts are mended, machines are modified, and new implements are fabricated. It is positioned next to a repair area and near a large door for working on outdoors projects. Ventilation, high quality lighting, multiple electrical outlets, and 220V electrical service are critical needs for metalworking welders, drills, grinders, torches and other stationary machines. Organizing the workflow in this space minimizes lifting and carrying materials around the shop. Store bulk metal near doors for restocking. Keep saws for rough sizing of material close to the bulk metal storage along with grinders, drill press, and machining tools. When there is enough room in the shop, steel from storage can be slid onto a lift cart, rolled to the saw, and lowered into position for cutting with little manual lifting. After cutting and machining, the workflows to the welder and then an assembly table with access to fastener assortments and tools.
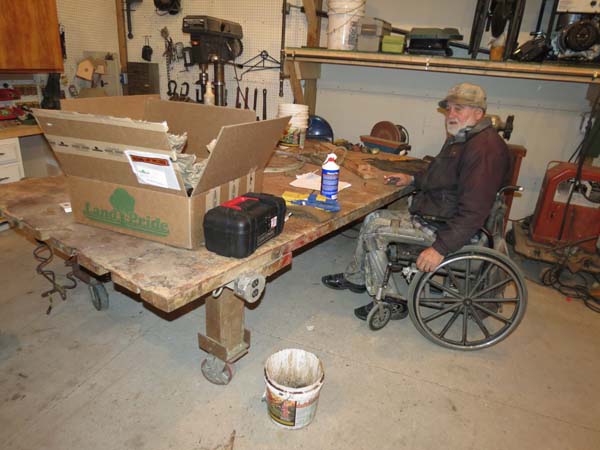
Figure 45. Workers using wheelchairs need to roll under and/or around the workbenches to reach the surfaces without bumping their legs or feet.
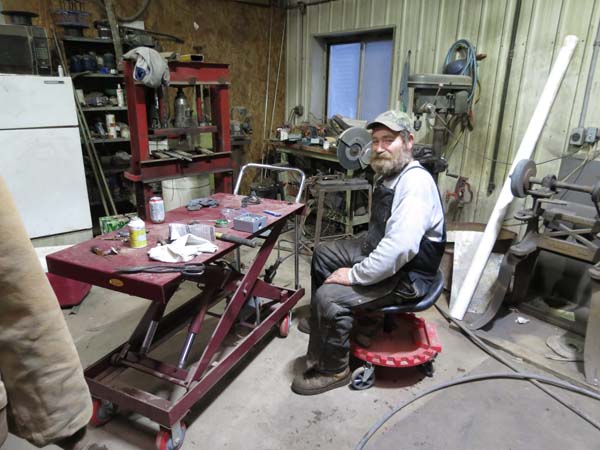
Figure 44. This farmer uses his hydraulic lift cart as an adjustable height worktable. In conjunction with his adjustable height shop stool, he can always work on a project from an ergonomic position.
A well-ventilated welding space with accessible tables and isolated from flammable material is a must for farm and ranch shops. Workers with nerve damage that causes numbness, such as from diabetes, should use extreme caution to prevent secondary injuries from burns and cuts. Use personal shielding, such as proper footwear, a leather welding apron, welder’s cap, and eye protection to minimize skin exposure. Auto-darkening and chin-operated welding helmets also help workers with arm impairments control their face shields. Magnifying lenses can be inserted into welding helmets for workers with low vision. Flammable items should be moved away and located in a fire-rated storage cabinet. A large ABC-rated fire extinguisher should be installed next to each welding table and access door in the event of fire.

Figure 46. This air compressor was raised from floor to table height with this foot-pumped hydraulic lift cart
without straining the farmer’s back.
Other workspaces may include painting or woodworking. Painting areas need excellent lighting, electrical outlets, ventilation fans with air filters, and racks for hanging parts. Fireproof storage cabinets for paint and flammable solvents should be in this area. Woodworking requires 220V electrical service, multiple outlets, and dust collection systems along with storage racks for lumber within easy reach. Worktables with hand tools, assorted screws, and hardware are valuable. As with all workspaces, ceiling mounted retractable cord reels and wide pathways around the area will allow access with mobility aids and portable tool carts.
General supply storage
Fasteners and other supplies should be organized and labeled for convenience in bins and stored close to the repairs and metalworking workspaces. Organizing service materials such as air filters, oil filters, and grease cartridges on shelves in specific categories makes maintenance less frustrating. Chemicals that need to be inside a shop should be secured and stored properly in their own designated storage area that is secure and fireproof. Minimize overhead storage that requires access using stairs or ladders. The most frequently used items should be stored 18” to 48” above the floor in storage areas. Least-used items and overflow inventory for later restocking should be placed on higher shelves farther from the workspace. (Friday, et.al, 1980). Storing heavy items on rolling furniture dollies or other mobile bases allows one to rearrange the shop for projects or cleaning without lifting and carrying.
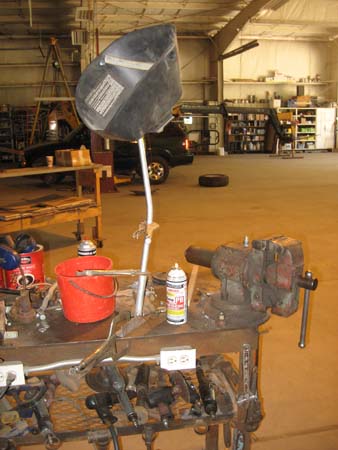
Figure 47. This welder’s workstation has a face
shield holder, tools underneath, and electrical
outlets.
Reducing clutter in the farm shop by removing over-supply and rarely used items is an important step in organizing. Avoid piling parts, pieces, tools, etc., in corners, on the floor, or on work benches. Grouping supplies into common areas of use makes a logical way to find stored items. Good housekeeping in the farm and ranch shop is critical for accessibility. Well organized supplies and clear pathways are helpful for a person with memory loss or low vision trying to find hardware or a person with a mobility aid walking in the workspace. Having places for tools and supplies on racks and off the floor enables easy routine cleaning of the shop facility. Oil spills can be cleaned, floors swept, and accumulated dust vacuumed with minimal obstructions.

Figure 48. Open bins with labels allow a quick visual scan to find hardware and supplies and identify needed restocking.
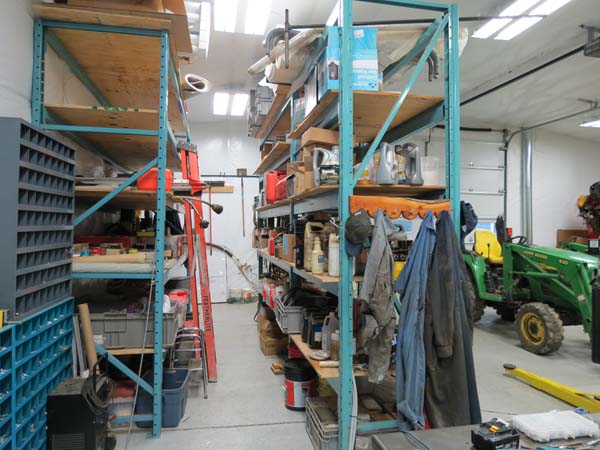
Figure 49. Pathways between storage racks need to be clear and uncluttered.
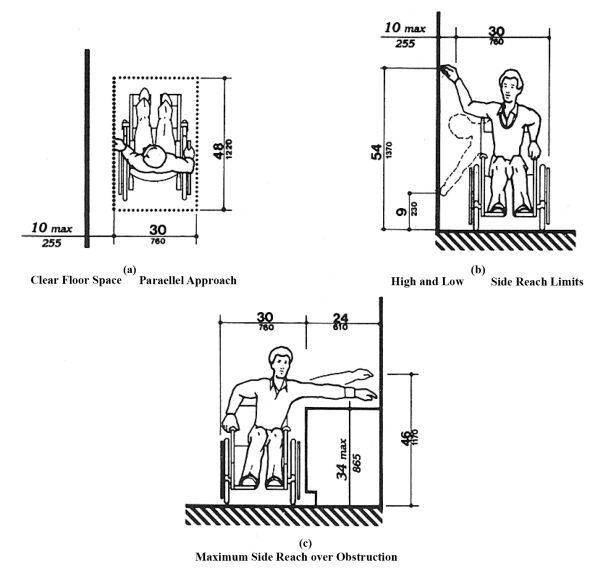
Figure 51. It is recommended to provide at least
three-feet for passage between stationary objects and five- feet work/maneuverability space around stationary workbenches and tools.
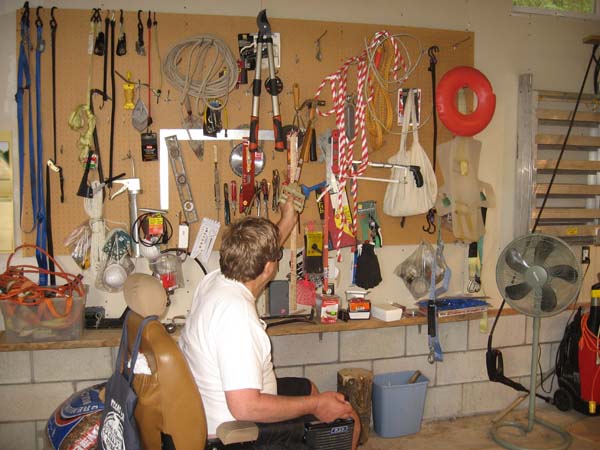
Figure 50. Pegboards can be a way to keep tools and maintenance supplies organized and visible instead of in out-of-sight locations.
Office and break room
The farm shop is a logical place for a designated office workspace outside the house. A whiteboard or clipboard in the office area is helpful for keeping a running
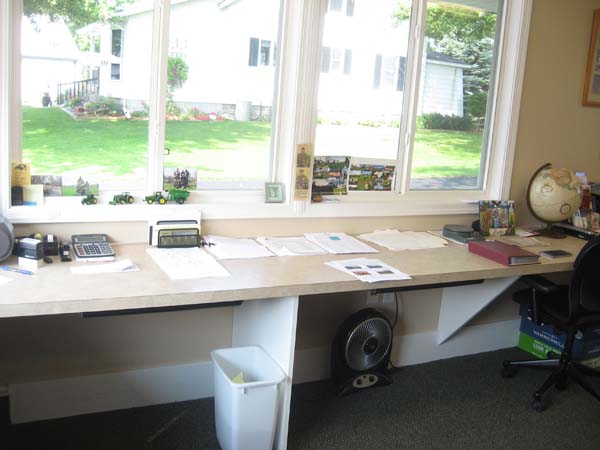
Figure 52. This farm office has roll-under desks and lowered
windows for looking out from a seated position.
list of needed supplies and repairs. Operator’s manuals, warranty information for tools or equipment, preventative maintenance schedules for specific farm equipment, materials safety data sheets (MSDS), checklists, and plans can be easily accessible for workers. Filing cabinets with labeled drawers can keep the paperwork organized, dry, and clean. A table with several chairs at which to sit is helpful for sketching, writing, or having meetings with farm workers.
A break room adds convenience for meals, especially during busy harvest or planting seasons. An accessible sink area with lever style faucets and clear space under it should be usable from a seated or standing position. A restroom and janitorial closet for cleaning supplies are also helpful. These can be good places for first aid kits and emergency preparedness supplies. Building a “roll-in” shower into the plans for the farm shop could reduce the amount of dirt tracked into the house and provide the means to shower – even for wheelchair users – following exposure to toxic chemicals. The task of keeping these spaces clean needs to be assigned to someone or the spaces may soon become unusable.
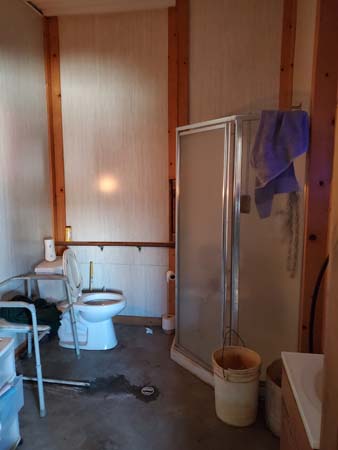
Figure 53. A restroom and shower with the break room increase efficiency of work in the farm shop and availability of a place to
wash down if there is chemical exposure.
The ability to contact first responders in the event of an emergency or to simply ask for assistance from a family member/coworker is necessary in the farm shop. All workers should carry a charged cell phone and understand how to make an emergency call. Many farm shops are metal-sided buildings in remote areas with poor phone service, so a cellular booster may be required for reliable communication. Consider “smart” home technologies in the shop, such as fire alarms, carbon monoxide detectors, thermostats, door controllers, remote cameras, and virtual AI assistants (Alexa, Siri, etc.). Voice assist devices are helpful in shop and office workspaces for keeping lists and operating lights or computers remotely. These devices can be used to warm up the shop before arrival, warn of unsafe conditions, and call for help. Smart security measures, such as remotely controlled lights, locks, and cameras, can be easily operated with a smartphone from anywhere in the world with internet connectivity. Designing these functions into the farm shop help make it useable for people of all abilities.
Funding Accessibility Renovations
When a farmer or rancher has an injury, illness, or disability, the accessibility of the farm shop becomes a
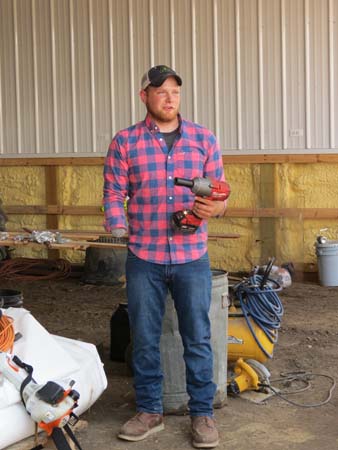
Figure 54. Working in the farm shop with one hand requires additional tools and sometimes costly assistive technology.
requirement, not merely a good idea. If the farm shop was not built with the unique needs of the farmer with the newly acquired disability in mind, renovations of the building structure may be needed along with the purchase of additional tools. Assistive tools, equipment, and work practices that enable a person with a disability to do necessary tasks are defined as assistive technology. Some of the common assistive technologies needed by farmers/ranchers have already been discussed and are available from multiple sources or might be modified locally. Some of these items are beyond the farmer’s budget and may require outside financial assistance.
One source that has been used successfully by many farmers and ranchers is Vocational Rehabilitation (VR). INSERT FIGURE 54. Each state has a vocational rehabilitation program to help people with disabilities prepare for, obtain, and maintain gainful employment. The purpose of the VR Program is to empower individuals with disability, particularly individuals with significant disability, to achieve high quality employment outcomes to which they aspire and that are consistent with their unique strengths, resources, priorities, concerns, abilities, capabilities, and informed choice. (U.S. Department of Education, 2004).
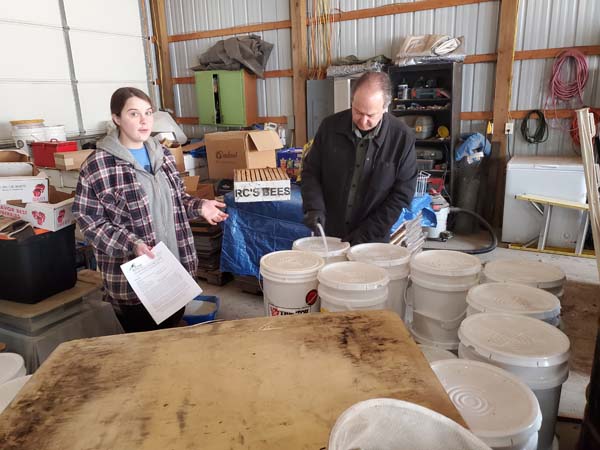
Figure 55. The vocational rehabilitation counselor and the farmer will work together to develop a plan for employment including services and assistive technology.
The first step in obtaining service from vocational rehabilitation is to contact the local office and complete its application for services. A vocational rehabilitation counselor will then work with the farmer or rancher to determine eligibility for services based on their disability and job goals. An assessment will often be done by an assistive technology professional (ATP) or occupational therapist (OT) to understand what accommodations are required to enable the worker to perform the necessary job tasks. The counselor and farmer/rancher will agree on the individual plan for employment and the services and assistive technology that may be needed. The U.S. Department of Education maintains a list of all the state vocational rehabilitation programs at https://rsa.ed.gov/about/states. Another source of assistance is the USDA AgrAbility Program. It has projects in more than 20 states that assist with enabling farm and ranch accessibility. For more information, visit www.agrability.org.
Conclusion
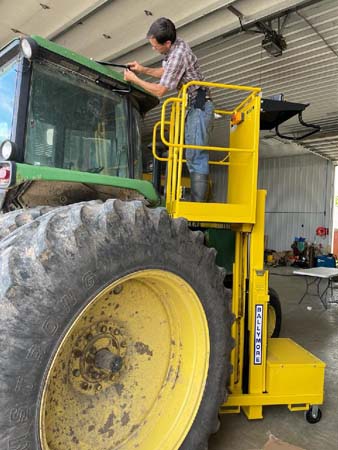
Figure 56. Universal design in the farm
shop increases everyone’s ability to
work more efficiently and with less
need to accommodate as workers grow
older or have medical impairments.
Whether building new or renovating, creating a space that accommodates the demands of the worker(s) is essential to farm shop accessibility, safety, and efficiency. Evaluate existing facilities and note the characteristics that need to be improved to safely accomplish necessary tasks. INSERT FIGURE 56 Seek recommendations from building trade professionals and home-improvement stores to consider the latest in building materials and finishings. Contact the state AgrAbility project or National AgrAbility Project for specific accessibility recommendations for the farm shop. These accessibility principles and a little ingenuity can make farm shops useable and efficient for most workers, regardless of age or disability.
Other resources
- The Toolbox Assistive Technology Database, agrability.org/toolbox
- Private industry (fellow farmers/ranchers)
- Iowa State University Extension, “Farm Shop Plans,” extension.iastate.edu/product/2709
- Successful Farming magazine, “Top Shops,” agriculture.com/machinery/top-shops
- Successful Farming magazine, “How to Design the Farm Shop for Your Future,” agriculture.com/how-to-design-the-farm-shop-for-your-future-8380234
- FBI Buildings, “Design the Perfect Farm Shop Plan: 3 Tips to Get Started,” fbibuildings.com/blog/farm-shop-plans
Cited References
Bausch, N.S. (2023, November 28). How to design the farm shop for your future. Successful Farming. November 28, 2023. Retrieved from www.agriculture.com/how-to-design-the-farm-shop-for-your-future-8380234
Bundy, D. & Harmon, D. (2009). Concrete Specifications for Agriculture. PM1589. Cooperative Extension Service. Iowa State University, Ames, IA. Retrieved from https://store.extension.iastate.edu/Product/Concrete-Specifications-for-Agriculture-Livestock-Industry-Facilities-and-Environment-PDF
Friday, W., Jones, D, Parsons, S. & Strickland, R. (1980). Planning Farm Shops for Work and Energy Efficiency. Pub. AE-104. Cooperative Extension Service, Purdue University, West Lafayette, IN. Retrieved from www.extension.purdue.edu/extmedia/ae/ae-104.html
Lechner, N., Lorenzen, R., Steinhardt, F., Conklin, G., Foss, E. (1981) Planning Farm Shops. Pub. NRAES-16. Cooperative Extension Service, Northeast Regional Agricultural Engineering Service, Cornell University, Ithaca, NY. Retrieved from https://blog.uvm.edu/cwcallah/files/2022/07/NRAES-16-Planning-Farm-Shops.pdf
National AgrAbility Project. (2011). The Toolbox Assistive Technology Database. Purdue University. West Lafayette, IN. Retrieved from www.agrability.org/toolbox.
OSHA. (1999). Ventilation Primer. OSHA Technical Manual (OTM) Appendix III:3-1. OSHA Directive TED 01-00-015 [TED 1-0.15A], Retrieved from www.osha.gov/otm/section-3-health-hazards/chapter-3#app3-1
U.S. Department of Education. (2004) 34 CFR 361.50: Written Policies Governing the Provisions of Services for Individuals with Disabilities. Retrieved from www.govinfo.gov/content/pkg/CFR-2004-title34-vol2/pdf/CFR-2004-title34-vol2-sec361-50.pdf
Reviewers
- Bill Field, National AgrAbility Project, Purdue University
- Ed Sheldon, National AgrAbility Project, Purdue University
- Paul Jones, National AgrAbility Project, Purdue University
- Kyle Haney, AgrAbility in Georgia, University of Georgia